-
Plastic Profile Extruder Machine
-
WPC Profile Extruder Machine
-
PVC Profile Extruder
-
PVC Panel Production Line
-
PVC Pipe Production Line
-
PVC Sheet Production Line
-
PE Sheet Extruder
-
PP Hollow Board Extrusion Line
-
Plastic Pipe Production Line
-
Plastic Sheet Extrusion Line
-
Plastic Board Extrusion Line
-
Plastic Pelletizing Machine
-
Plastic Auxiliary Equipment
Automatic Door Window U-PVC Profile Production Line UPVC Plastic Profile Extruder
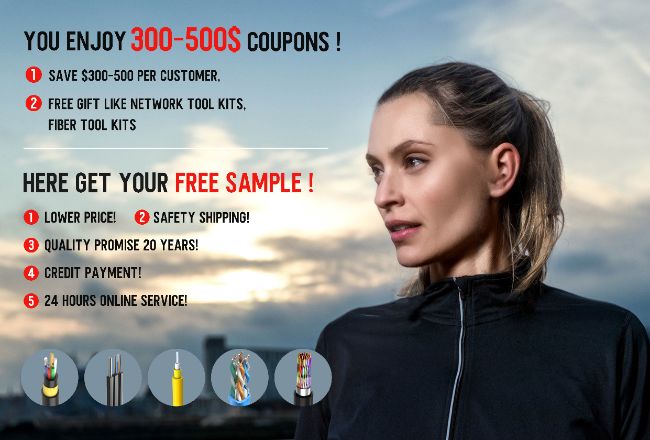
Contact me for free samples and coupons.
Whatsapp:0086 18588475571
Wechat: 0086 18588475571
Skype: sales10@aixton.com
If you have any concern, we provide 24-hour online help.
xName | UPVC Door Window Profile Production Line | Color | Green,Other Colors Can Be Customized |
---|---|---|---|
Material | UPVC | Capacity | 80-400kg/h,Other Capcity Can Be Customized |
Motor Power | 22-55KW,Other Power Can Be Customized | Power | 220V/380V,Other Power Can Be Customized |
Control System | PLC | Payment | T/T |
Highlight | UPVC Plastic Profile Making Extruder,55KW UPVC Plastic Profile Extruder,380V Plastic Profile Extruder Machine |
Fully Automatic Cheap Price U-PVC Door Window Profile Production Line UPVC Plastic Profile Making Extruder Machine
UPVC Door And Window Profile Production Line
1. Production Introduction
The UPVC door and window profile production line is an automated production equipment used to manufacture door and window frames made of UPVC (inorganic chlorinated polyvinyl chloride) material. UPVC material is a plastic material widely used in door and window manufacturing and is favored for its weather resistance, thermal insulation, anti-corrosion and durability.
2. Production Feature
(1) Automated production: The UPVC door and window profile production line uses automated equipment and control systems to achieve a highly automated production process. This can improve production efficiency and product quality, and reduce labor input and human errors.
(2) High-precision processing: The production line is equipped with advanced processing equipment, capable of high-precision material cutting, shaping and processing. This ensures dimensional accuracy and consistency of door and window profiles.
(3) Multifunctional production: UPVC door and window profile production lines usually have multiple functional modules and can produce door and window profiles of different specifications and types. The production line can be adjusted and configured as needed to meet the needs of different customers.
(4) Efficient energy consumption: The production line is designed with energy efficiency in mind, using energy-saving equipment and processes to reduce energy consumption and environmental impact.
(5) Quality control: The production line is equipped with a quality control system to monitor and control key parameters during the production process to ensure stable product quality. This avoids production defects and reduces scrap rates.
(6) Flexibility and scalability: UPVC door and window profile production lines usually have flexible configuration and scalability, and can be adjusted and expanded according to market demand. This enables the production line to adapt to production of different sizes and needs.
3. Production Configuration
Equipment Model |
Motor Power |
Capacity |
Total Power |
KSJSZ-51/105 |
22KW | 80-150kg/h | 55KW |
KSJSZ-65/132 |
37KW | 180-240kg/h | 80KW |
KSJSZ-80/156 |
55KW | 350-400kg/h | 110KW |
Note: In addition to the above configurations, our company can also customize according to customer needs.
4. Payment
30% as advance payment by T/T after signed contract; 70% as balance before delivery by T/T.
5. The seller will provide the actual electric, pneumatic, hydraulic, mechanical parts circuit diagram for each unite of the machine with English language in addition to the original operation manual of the machine that contains the operation instruction, safety instruction, and troubleshooting with parts list for easy order necessary spare parts in the future.
6. Test run in the buyer’s factory: Seller send engineer for supervision of installation, training and test. The test will be finished in about 7-10 days if necessary preparations are made by the buyer such as water, electricity. Materials, work space, labors and so on. The round airplane tickets, visa cost, food, hotel fee and medical insurance of the engineer for installation and test run are paid by the buyer. The buyer pay USD150/per day as subsidy for the engineer.