-
Plastic Profile Extruder Machine
-
WPC Profile Extruder Machine
-
PVC Profile Extruder
-
PVC Panel Production Line
-
PVC Pipe Production Line
-
PVC Sheet Production Line
-
PE Sheet Extruder
-
PP Hollow Board Extrusion Line
-
Plastic Pipe Production Line
-
Plastic Sheet Extrusion Line
-
Plastic Board Extrusion Line
-
Plastic Pelletizing Machine
-
Plastic Auxiliary Equipment
Fully Automatic ASA PE PP PVC Single Screw Plastic Extruder For Sale PVC Profile Extruder
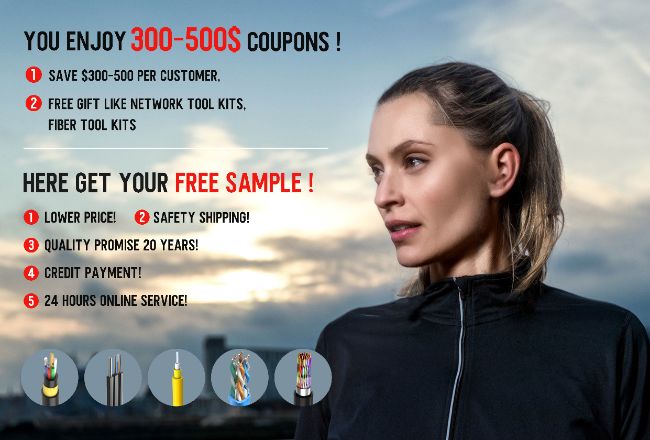
Contact me for free samples and coupons.
Whatsapp:0086 18588475571
Wechat: 0086 18588475571
Skype: sales10@aixton.com
If you have any concern, we provide 24-hour online help.
xName | ASA PE PP PVC Single Screw Plastic Extruder | Material | ASA PE PP PVC |
---|---|---|---|
Color | Green | Control System | PLC |
Material Of Barrel | 38CrMoAlA | Material Of Screw | 38CrMoAlA |
Voltage | 380V/50Hz/3Phase | Weight | 3000-5000kg |
ASA PE PP PVC Single Screw Plastic Extruder
1. Production Introduction
ASA, PE, PP and PVC are common plastic materials used in various extrusion processes. A single-screw extruder is a commonly used extrusion equipment used to push molten plastic material through a die to produce the desired shape and size.
2. The following is a brief introduction to ASA, PE, PP and PVC single screw extruders:
(1) ASA (Acrylonitrile-Butadiene-Styrene Copolymer): ASA is a copolymer with good UV resistance and weather resistance. It is widely used in outdoor applications such as building materials, automotive parts, and electrical enclosures. The extrusion processing of ASA usually needs to be carried out at higher temperatures to ensure that the material can fully melt and flow.
(2) PE (polyethylene): Polyethylene is a common plastic material with good chemical stability and electrical insulation properties. It is widely used in packaging materials, pipes, wire insulation and household products. The extrusion processing of PE usually needs to be carried out at lower temperatures to avoid material decomposition or overheating.
(3) PP (polypropylene): Polypropylene is a plastic material with excellent mechanical properties and chemical stability. It is widely used in packaging materials, pipes, containers and automotive parts. The extrusion processing temperature of PP is usually higher to ensure complete melting and flow of the material.
(4) PVC (polyvinyl chloride): Polyvinyl chloride is a common plastic material with good corrosion resistance and flame retardant properties. It is widely used in construction materials, cable insulation, pipes and household products. The extrusion processing of PVC usually needs to be carried out at higher temperatures, and stabilizers are added to improve the thermal stability of the material.
Single-screw extruder is a commonly used extrusion equipment, including screw, barrel and heating/cooling system. During the extrusion process, plastic particles are added to the screw feed port, and then through the rotation of the screw and the heating of the heating system, the plastic is melted and pushed into the mold. The shape of the mold determines the final form of the extruded product.
Single-screw extruders are suitable for extrusion processing of various plastic materials, including ASA, PE, PP and PVC. The extrusion process of different materials may require different temperature, pressure and speed parameters to ensure the best extrusion effect and product quality.
3. Production Feature
(1) Versatility: Single-screw extruders can be applied to a variety of plastic materials, including ASA, PE, PP, and PVC. This makes them widely applicable in different industries and applications.
(2) Flexibility: These extruders can adapt to the needs of different materials by adjusting process parameters, such as temperature, screw speed, and feed rate. This flexibility allows the production process to be adjusted to meet the requirements of different products.
(3) High efficiency: The single-screw extruder has efficient plasticizing and extrusion capabilities and can achieve continuous production. They generally have higher extrusion output and lower energy consumption, improving production efficiency.
(4) Stability: These extruders have stable operating characteristics and optimized control systems that ensure the stability and consistency of the extrusion process. This helps improve product quality and reduce variation in production.
(5) Equipment reliability: ASA, PE, PP and PVC single-screw extruders are usually made of high-quality materials and have sturdy and durable structures. They are carefully designed and manufactured to meet the requirements of high-intensity operation over long periods of time.
(6) Ease of operation: These extruders are often equipped with intuitive operating interfaces and user-friendly control systems that allow operators to easily adjust and monitor the extrusion process.
(7) Support customization: The single-screw extruder can be customized according to the specific needs of the customer, including the size of the extruder, screw structure and control system, etc. This can meet the specific production requirements of different customers.
Overall, ASA, PE, PP and PVC single-screw extruders offer versatility, flexibility, high efficiency, stability, equipment reliability, ease of operation and customization support, making them the most popular in the plastics processing industry. Commonly used extrusion equipment.
4. Production Configuration
Equipment Model | Motor Power |
KSJSZ-51/105 | 22KW |
KSJSZ-65/132 | 37KW |
KSJSZ-80/156 | 55KW |
5. Payment
30% as advance payment by T/T after signed contract; 70% as balance before delivery by T/T.
6. The seller will provide the actual electric, pneumatic, hydraulic, mechanical parts circuit diagram for each unite of the machine with English language in addition to the original operation manual of the machine that contains the operation instruction, safety instruction, and troubleshooting with parts list for easy order necessary spare parts in the future.
7. Test run in the buyer’s factory: Seller send engineer for supervision of installation, training and test. The test will be finished in about 7-10 days if necessary preparations are made by the buyer such as water, electricity. Materials, work space, labors and so on. The round airplane tickets, visa cost, food, hotel fee and medical insurance of the engineer for installation and test run are paid by the buyer. The buyer pay USD150/per day as subsidy for the engineer.