-
Plastic Profile Extruder Machine
-
WPC Profile Extruder Machine
-
PVC Profile Extruder
-
PVC Panel Production Line
-
PVC Pipe Production Line
-
PVC Sheet Production Line
-
PE Sheet Extruder
-
PP Hollow Board Extrusion Line
-
Plastic Pipe Production Line
-
Plastic Sheet Extrusion Line
-
Plastic Board Extrusion Line
-
Plastic Pelletizing Machine
-
Plastic Auxiliary Equipment
SJSZ Series Conical Twin Barrel Screw Extruder For Plastic Auxiliary Equipment
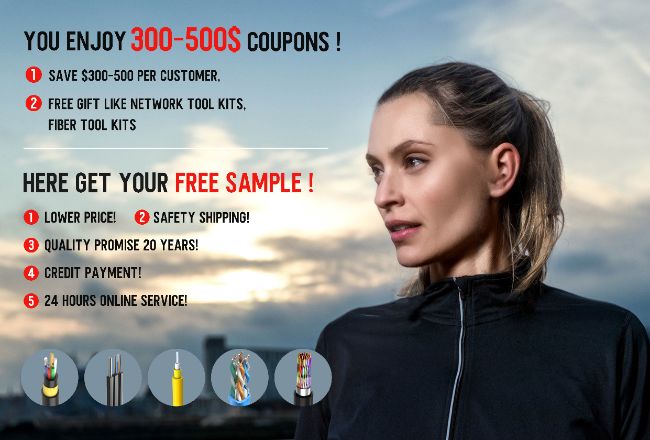
Contact me for free samples and coupons.
Whatsapp:0086 18588475571
Wechat: 0086 18588475571
Skype: sales10@aixton.com
If you have any concern, we provide 24-hour online help.
xName | SJSZ Series Conical Double/Twin Barrel Screw Extruder | Color | Green |
---|---|---|---|
Number Of Screw | 2 Pcs | Center Height | 1000mm |
Diection Of Screws | Screw Rotation Direction | Voltage | 220V,Other Voltage Can Be Customized |
Warranty | 1 Year | Payment | T/T |
Highlight | Conical Twin Barrel Screw Extruder,SJSZ Series Screw Extruder,Plastic Auxiliary Equipment Extruder Machine |
High Quality SJSZ Series Conical Double/Twin Barrel Screw Extruder Used For Plastic Machine Plastic Auxiliary Equipment
SJSZ Series Conical Double/Twin Barrel Screw Extruder
1. Production Introduction
A conical twin screw extruder is an equipment used for plastic extrusion processing, which adopts a twin screw structure, where the screw is conical. This type of extruder is often used to manufacture plastic pipes, plates, particles, and other products.
2. Production Configuration
Equipment Model |
Screw Rotation Speed (rpm) |
Main Motor Power |
Capacity |
KSJSZ-45 |
1-45 | 15kw | 120kg/h |
KSJSZ-51 |
1-45 | 18.5kw | 80-150kg/h |
KSJSZ-55 |
40 | 22/30kw | 150-180kg/h |
KSJSZ-65 |
1-35 | 37kw | 250-300kg/h |
KSJSZ-80 |
1-37 | 55kw | 320-400kg/h |
KSJSZ-92 |
1-33 | 90kw | 600-800kg/h |
Note: In addition to the above configurations, our company can also customize according to customer needs.
3. Working Principle:
(1) Feeding and heating: The raw materials enter the screw groove of the extruder through the feeding port, and are preheated through the heating system to reach the appropriate plasticizing temperature.
(2) Mixing and plasticization: The rotation of the screw drives the raw material forward, and the material gradually melts and mixes under the stirring and heating action of the screw, forming a uniform molten substance.
(3) Pressure and extrusion: As the screw rotates, the material is subjected to gradually increasing pressure in the conical screw groove, and finally extruded through the opening of the mold to form the desired product shape.
(4) Cooling and solidification: The extruded product passes through a cooling device, such as a water bath or cooling airflow, to quickly cool and solidify, maintaining the desired shape and size.
4. Production Feature
(1) Twin screw structure: The conical twin screw extruder is operated by two screws in parallel, allowing for better mixing and plasticization of materials during the extrusion process.
(2) Conical design: The screw has a conical design, and the pitch gradually decreases, increasing the pressure and shear effect of the extruder, which is conducive to the plasticization and extrusion of materials.
(3) High efficiency: The conical twin screw extruder has large processing capacity and high extrusion speed, suitable for large-scale and high-yield production needs.
(4) Suitable for different materials: The conical screw extruder is suitable for processing various plastic materials, such as polyethylene (PE), polyvinyl chloride (PVC), polypropylene (PP), etc.
5. Payment
30% as advance payment by T/T after signed contract; 70% as balance before delivery by T/T.
6. The seller will provide the actual electric, pneumatic, hydraulic, mechanical parts circuit diagram for each unite of the machine with English language in addition to the original operation manual of the machine that contains the operation instruction, safety instruction, and troubleshooting with parts list for easy order necessary spare parts in the future.
7. Test run in the buyer’s factory: Seller send engineer for supervision of installation, training and test. The test will be finished in about 7-10 days if necessary preparations are made by the buyer such as water, electricity. Materials, work space, labors and so on. The round airplane tickets, visa cost, food, hotel fee and medical insurance of the engineer for installation and test run are paid by the buyer. The buyer pay USD150/per day as subsidy for the engineer.