-
Plastic Profile Extruder Machine
-
WPC Profile Extruder Machine
-
PVC Profile Extruder
-
PVC Panel Production Line
-
PVC Pipe Production Line
-
PVC Sheet Production Line
-
PE Sheet Extruder
-
PP Hollow Board Extrusion Line
-
Plastic Pipe Production Line
-
Plastic Sheet Extrusion Line
-
Plastic Board Extrusion Line
-
Plastic Pelletizing Machine
-
Plastic Auxiliary Equipment
Hot And Cold Water Plumbing PPR PP PE Plastic Pipe Production Line Extruder
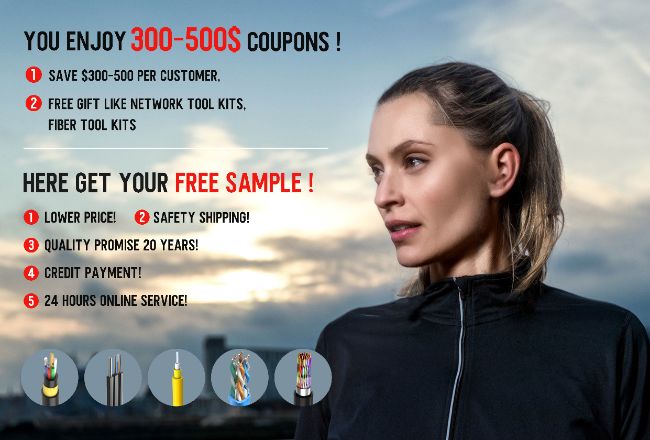
Contact me for free samples and coupons.
Whatsapp:0086 18588475571
Wechat: 0086 18588475571
Skype: sales10@aixton.com
If you have any concern, we provide 24-hour online help.
xScrew Design | Single-screw | Plastic Processed | PE, PP, PPR |
---|---|---|---|
Application | PIPE | Key Selling Points | High Productivity |
Core Components | Bearing, Motor, Pump, Gear, PLC, Pressure Vessel, Engine, Gearbox, Screw | Voltage | 380V 50HZ 3Phase(Customized) |
Final Product | PP PE PPR Pipe | Warranty | 1 Year Warranty |
Highlight | PPR Plastic Pipe Production Line,PE Cold Water Plumbing Extruder,380V PP Plastic Pipe Extruder |
Hot And Cold Water Plumbing Special PPR Pipe Machines Plastic PP PE Pipe Extrusion Line Manufacturer Extruder Equipment
一,The PPR pipe production line is a combination of equipment and processes used to manufacture polypropylene random copolymer (PPR) pipes. PPR pipe is a commonly used pipeline material with excellent heat resistance, corrosion resistance, and pressure resistance, widely used in water supply, heating, chemical and other fields. The following is a general introduction to the PPR pipe production line:
Model | Diameter(mm) | Main Motor | Max.output(KG/H) | Max.speed(M/MIN) | Total Power(KVA) |
SJ65/33 | 16-63 | 37 | 120 | 15 | 60 |
SJ90/33 | 75-160 | 55 | 200 | 10 | 130 |
1. Raw material preparation: The first step in the PPR pipe production line is to prepare the raw materials. The main raw materials include polypropylene (PPR) particles, fillers, stabilizers, etc. These raw materials are mixed and pre-treated according to specific formulas.
2. Extruder: The mixed raw materials are heated, plasticized, and extruded through an extruder. The extruder is composed of a feeding section, a screw, a cylinder, and a die head. The screw pushes the molten raw material into the mold head to form the desired pipe shape.
3. Cooling water tank: The molten raw material pipes from the extruder pass through the cooling water tank to quickly cool and solidify. A cooling water tank is usually a rectangular tank that maintains a certain cooling effect through water circulation.
4. Straightening machine: The cooled and solidified pipes are straightened and trimmed through the straightening machine to ensure the diameter and dimensional accuracy of the pipes.
5. Cutting machine: The straightened pipe is regularly cut into the required length by the cutting machine. The cutting machine can be manually operated or automated.
6. Hot melt connection: PPR pipes can be connected to the pipeline system through hot melt connection. Hot melt connection is the process of heating the end of a pipe to a molten state, then quickly connecting it to cool and solidify, forming a solid connection.
The PPR pipe production line is usually automated and can be customized and adjusted as needed. The scale and production capacity of the production line can be designed according to demand, and there are different configuration options from small production lines to large factories.
Overall, the PPR pipe production line achieves an efficient, stable, and reliable PPR pipe production process through processes such as raw material processing, extrusion, cooling and shaping, cutting and stacking, and quality control. These pipes are widely used in fields such as construction engineering, water supply systems, heating systems, and chemical pipelines, and have excellent heat resistance, pressure resistance, and chemical corrosion resistance.
二,PAYMENT TERMS
30% of total amount should be paid by T/T as down payment. The balance (70% of total amount) should be paid before delivery by T/T or irrevocable L/C by payment (at sight)
三,Delivery conditions
1. delivery condition: FOB Qingdao port.
2. delivery term: within 45 working days after receipt of down payment, the seller should inform the buyer to do inspection. The seller should finish packing of goods and ready for shipment within 15 working days after the seller receipt the full payment.
3. supervision of loading: the seller should inform the buyer exacting loading time, the buyer should arrange for supervision of loading!
四,INSPECTION
The seller should inform the buyer to do inspection before shipment, the seller guaranty good performance of all the sold goods. The seller undertake the material cost for the machine inspection in seller's factory. The buyer should come to seller's factory to do the inspection work, or the buyer could entrust any third part to come to seller's factory to do the inspection work.
五,INSTALLATION
The seller should send engineer to buyer's factory for machine installation and testing. Buyer should undertake all the traveling costs for engineer (such as hotel, air tickets and food) and engineer salary 200 USD/day/engineer. If engineers can't go to customer's factory for machine installation, the seller should provide online video calling service to guide customer for machine installation and running.