-
Plastic Profile Extruder Machine
-
WPC Profile Extruder Machine
-
PVC Profile Extruder
-
PVC Panel Production Line
-
PVC Pipe Production Line
-
PVC Sheet Production Line
-
PE Sheet Extruder
-
PP Hollow Board Extrusion Line
-
Plastic Pipe Production Line
-
Plastic Sheet Extrusion Line
-
Plastic Board Extrusion Line
-
Plastic Pelletizing Machine
-
Plastic Auxiliary Equipment
PVC Pipe Processing Machine Plastic Pvc Pipe Production Line for Hotels
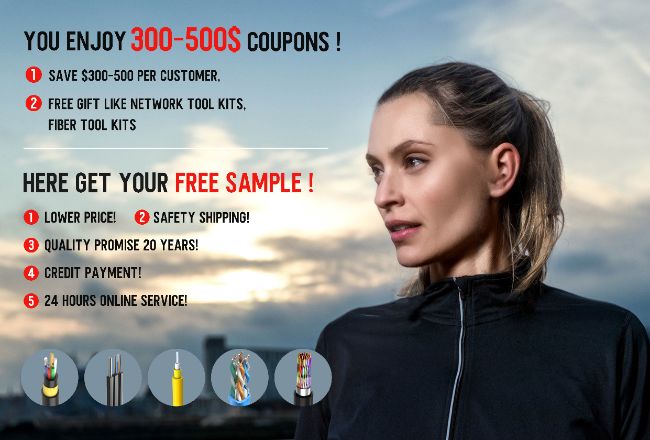
Contact me for free samples and coupons.
Whatsapp:0086 18588475571
Wechat: 0086 18588475571
Skype: sales10@aixton.com
If you have any concern, we provide 24-hour online help.
xScrew Design | Double-screw | Plastic Processed | PVC |
---|---|---|---|
Applicable Industries | Hotels, Garment Shops, Building Material Shops, Manufacturing Plant, Machinery Repair Shops, Food & Beverage Factory, Farms, Restaurant, Home Use, Retail, Food Shop, Printing Shops, Construction Works , Energy & Mining, Food & Beverage Shops, Advertising C | Core Components | Bearing, Motor, Pump, Gear, PLC, Pressure Vessel, Engine, Gearbox, Screw |
Voltage | 380V 50HZ 3Phase(Customized) | Raw Material | PVC Powder |
Application | PIPE | Key Selling Points | High Productivity |
Highlight | 380V Pvc Pipe Production Line,380V Pvc Pipe Production Line,Double Screw PVC Pipe Extruder |
KE CHENG DA pvc pipe making machine pipe processing machines plastic extruders pipe production line
The PVC (polyvinyl chloride) pipe production line is a combination of equipment and processes used to manufacture PVC pipes. PVC pipes are widely used in fields such as construction, water supply and drainage, power, communication, and farmland irrigation. The following is a general introduction to the PVC pipe production line:
1. Raw material preparation: The first step in the PVC pipe production line is to prepare the raw materials. The main raw materials are polyvinyl chloride resin powder (PVC resin), as well as additives such as stabilizers, lubricants, fillers, etc. These raw materials are mixed and pre-treated according to specific formulas.
2. Extruder: The mixed PVC raw materials are heated and plasticized through an extruder, resulting in an extruded molten state. The extruder is composed of a feeding section, a screw, a cylinder, and a die head. The screw pushes the molten PVC into the mold head, forming the desired pipe shape.
3. The extruded pipe enters the cooling device through a conveyor belt or roller to quickly cool and solidify. Then, enter the sizing machine and control the outer diameter and wall thickness of the pipe through molds of different specifications.
4. The final step of the production line is to conduct quality inspection and packaging of the finished product. Inspect the dimensions, appearance, mechanical properties, and other aspects of the pipes to ensure that the products meet quality standards. Then, the pipes are usually packaged in a form suitable for transportation and storage.
Model | PVCG-2-50 | PVCG-4-25 | PVCG-110 | PVCG-160 | PVCG-250 | PVCG-315 | PVCG-400 | PVCG-6630 |
Supporting Extruder | SJZ51/105 | SJZ665/132 | SJZ51/105 | SJZ65/132 | SJZ65/132 | SJZ80/156 | SJZ80/156 | SJZ92/188 |
Pipe Range(mm) | 16-50 | 16-25 | 20-110 | 50-160 | 50-250 | 110-315 | 160-400 | 315-630 |
The length of vacuuum calibration tank(mm) | 4000 | 4000 | 6000 | 6000 | 6000 | 6000 | 6000 | 6000 |
Haul-off speed(m/min) | 1.2-12 | 1-10 | 0.6-6 | 0.5-5 | 0.4-4 | 0.3-3 | 0.2-2.5 | 0.2-1.5 |
Installed capacity(kw) | 67 | 85 | 67 | 85 | 95 | 125 | 135 | 255 |
Total length(mm) | 17000 | 18000 | 17000 | 18000 | 20000 | 20500 | 28000 | 30000 |
In addition to the basic process steps mentioned above, some PVC pipe production lines may also include other processes, such as vacuum straightening, wire cutting, thread processing, etc., to meet the needs of different pipeline applications. In addition, some production lines may integrate automated control systems to improve production efficiency and product quality.
Perfect service system:
1. We will provide the Feasibility Analysis Report for the wood-plastic project.
2. We will provide the model selection and technical parameter for wood-plastic machinery.
3. We will provide the design for the plant and electric power accounting for the facilities.
4. We will provide the design for wood-plastic formula according to the product requirements.
5. We will provide the technology of wood-plastic product surface treatment
6. We will provide technique training for operator.
7. We will provide solution for the practical problem during the production.
8. We will install and test the machine for free.
9. We will provide turnkey project to customers.