-
Plastic Profile Extruder Machine
-
WPC Profile Extruder Machine
-
PVC Profile Extruder
-
PVC Panel Production Line
-
PVC Pipe Production Line
-
PVC Sheet Production Line
-
PE Sheet Extruder
-
PP Hollow Board Extrusion Line
-
Plastic Pipe Production Line
-
Plastic Sheet Extrusion Line
-
Plastic Board Extrusion Line
-
Plastic Pelletizing Machine
-
Plastic Auxiliary Equipment
PP Hollow Sheet Extruder Recycled Plastic Polypropylene Corrugated Board Extrusion Line
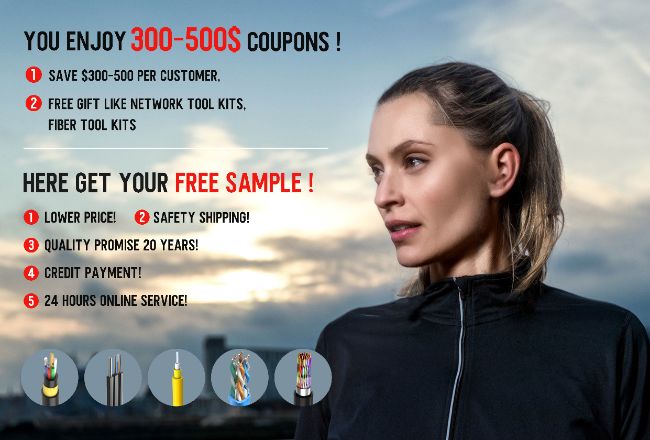
Contact me for free samples and coupons.
Whatsapp:0086 18588475571
Wechat: 0086 18588475571
Skype: sales10@aixton.com
If you have any concern, we provide 24-hour online help.
xName | PP Hollow Board Extrusion Line | Material | PP |
---|---|---|---|
Color | Green,Other Colors Can Be Customized | Control System | PLC Control |
Main Motor Power | 75KW,50KW,Other Power Can Be Customized | Max. Output | 60-300kg/h,Other Output Can Be Customized |
Width Of Sheet | 600-2100mm,Other Width Can Be Customized | Payment | T/T |
Highlight | PP Hollow Sheet Extruder,Polypropylene Corrugated Board Extrusion Line,Recycled PP Hollow Sheet Extruder |
High Quality PP Hollow Sheet Extruder Recycled Plastic Polypropylene Corrugated Board Extrusion Line Manufacturer
PP Hollow Board Extrusion Line
1. Production Intruduction
The PP hollow grid board production line is a specialized equipment used to manufacture hollow grid boards of polypropylene (PP) materials. PP hollow grid board has the characteristics of lightweight, high strength, corrosion resistance, waterproof and moisture-proof, and is widely used in fields such as construction, packaging, logistics, and agriculture.
2. Production Feature
(1) Automated production:
The PP hollow grid board production line adopts automated equipment and control systems to achieve automated operations throughout the entire production process, reduce manual intervention, and improve production efficiency and product consistency.
(2) Flexibility and adjustability:
The production line can be adjusted and optimized according to customer needs to adapt to the production of PP hollow grid boards of different specifications, sizes, and shapes. Flexible replacement of molds and adjustment of extruder parameters to meet diverse market demands.
(3) High quality products:
The PP hollow grid board production line adopts advanced production processes and technologies to ensure stable product quality and performance. Through precise control and monitoring systems, the dimensional accuracy, appearance quality, and physical performance of products can be guaranteed.
(4) Efficient and energy-saving:
The production line adopts high-efficiency extruders and cooling equipment to maximize production efficiency and energy utilization efficiency. Optimized heating and cooling systems can reduce energy consumption and production costs.
(5) Easy operation and maintenance:
The operation interface of the production line usually adopts a human-machine interface, which is easy and intuitive to operate. At the same time, the equipment structure is reasonable, easy to maintain and maintain, reducing the downtime and maintenance costs of the production line.
(6) Environmental protection and sustainability:
The PP hollow grid board production line adopts a pollution-free production process, without VOC emissions and hazardous waste generation. The use of polypropylene materials can reduce the consumption of natural resources and has the characteristics of environmental protection and sustainable development.
(7) Multifunctionality:
The PP hollow grid board production line can produce various specifications and shapes of hollow grid boards, suitable for different application fields and industries. We can customize production according to customer needs to meet diverse market demands.
3. Production Configuration
Model | Width | Main Motor | Capcity | Total Powwer |
SJ90 | 600-1300mm | 75KW | 60-190kg/h | 180kw |
SJ120 | 800-2100mm | 90KW | 120-300kg/h | 225kw |
Note: In addition to the above equipment, our company can also customize according to customer needs.
4. Payment
30% paid by T/T as down payment the balance (70%)should be paid before delivery (by T/T )
5. The seller will provide the actual electric, pneumatic, hydraulic, mechanical parts circuit diagram for each unite of the machine with English language in addition to the original operation manual of the machine that contains the operation instruction, safety instruction, and troubleshooting with parts list for easy order necessary spare parts in the future.
6. Test run in the buyer’s factory: Seller send engineer for supervision of installation, training and test. The test will be finished in about 7-10 days if necessary preparations are made by the buyer such as water, electricity. Materials, work space, labors and so on. The round airplane tickets, visa cost, food, hotel fee and medical insurance of the engineer for installation and test run are paid by the buyer. The buyer pay USD100/per day as subsidy for the engineer.